07.03.19
Messlösungen für die faseroptische Fertigung
Lichtleiterkabel stellen an die Inline-Messtechnik besondere Anforderungen. Dies liegt an den extrem kleinen Abmessungen der Faser selbst und an den Toleranzen im Submikronbereich beim Ziehen und Beschichten.
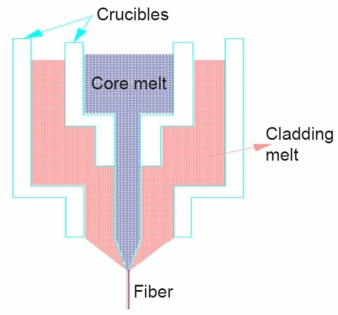
Beim Doppeltiegel-Verfahren wird das geschmolzene Kernglases durch einen inneren Tiegel gezogen sowie das geschmolzene Umhüllungsglases durch einen äußeren Tiegel. Hauptvorteil dieser Methode ist, dass unendlich lange Fasern gezogen werden können, solange die Tiegel ständig nachgefüllt werden. Sogar Step-/Graded-Index-Fasern lassen sich ziehen. © Zumbach
Zumbach Electronics bietet Messlösungen zu fast allen faseroptischen Fertigungsschritte an wie für
– Durchmesser, Ovalität und Position beim Ziehen der Faser
– Beschichten
– Loose-Tubing
– Extrudieren des Außenmantels sowie für die
– Herstellung von Zugelementen aus Stahl oder „Kevlar“.
1. Bei Glasfaserkabeln wird Quarzsand zur so genannten Vorform geformt. Hierbei handelt es sich um ein hochwertiges Glasrohr mit nahezu perfekter Oberfläche und Wandstärke sowie Rundlaufgenauigkeit.
2. Bei der Herstellung des Vorformlings wird typisch ein Drehprozess verwendet, bei dem Präzisionsinstrumente erforderlich sind, um den Außendurchmesser zu ermitteln, wodurch Prozessdaten zur Maschine zurückgeleitet werden zwecks kontinuierlicher Kontrolle. Dies wird in der Regel mit Scanning-Lasermessgeräten durchgeführt. Da der Prozesstemperaturen jenseits 2000 °C vorkommen, muss jedes Instrument für die Installation vorbereitet werden.
3. Die fertige Vorform wird einem Turm montiert, der zur Extrusion dient. Dabei wird intensive Wärme auf die Basis der Vorform gerichtet, wodurch diese schmilzt und ein Tröpfchen bildet. Die Faser nimmt ihre Form an.
4. Das Tröpfchen wird am unteren Rand des Schubkasten-Turms von einer Windeeinheit erfasst, die als Ziehstation dient. Die Vorform wird durch ein Antriebssystem in den erwärmten Bereich am oberen Ende des Schubladenturms eingeführt, um ein kontinuierliches Tröpfchen und somit eine kontinuierliche Faser mit gleichem Durchmesser aufrechtzuerhalten.
5. Durch den Ziehvorgang ist die Positionierung des Vorformlings hinsichtlich der Heizeinrichtung kritisch, um eine konzentrische und perfekt runde Faser zu gewährleisten. Dies wird durch mehrere Servoantriebe erreicht, die den Vorformling durch den erwärmten Bereich führen, gleichzeitig aber seine zentrale Position in einem Zwei-Achsen-Format (X und Y) ausgleichen. Um den Prozess zu optimieren, sind Laser-Durchmesser-Messgeräte unerlässlich. Sie messen die Durchmesser in mehreren Achsen, können direkt mit den beweglichen Achsen der Zugtürme in Verbindung stehen und melden die optische Position in Bezug auf die wahre Mitte der Schubladentürme zurück. Die Leistung einer Faser hängt direkt zusammen mit ihrer Gleichmäßigkeit in Abmessung und Querschnitt.
6. Im gleichen Prozess werden mehrere Farbkennzeichnung-Schichten aufgebracht. Aushärteöfen stellen sicher, dass die Farben trocken sind, bevor ein Kontakt mit weiteren Verarbeitungsgeräten hergestellt wird. Spezielle Durchmessermessgeräte werden eingesetzt, um eine gleichmäßige Oberflächenbeschichtung sicherzustellen. Schließlich wird ein Gerät verwendet, um eventuelle Oberflächenfehler wie – beispielsweise – fehlende Beschichtung zu erfassen oder Gele in der Beschichtung, Blasen oder Kratzer.
7. Die fertige Faser wird auf Trommeln auf die erforderliche Länge aufgewickelt, die mehr als 3 km betragen kann.
8. Optische Fasern werden in der Regel in Bündeln zusammengefasst, die für ihre endgültige Anwendung spezifisch sind, wobei es darauf ankommt, sicherzustellen, dass keine Verspannung, Verbiegung oder Knickung auftritt, wodurch die Gefahr besteht, dass die zugrunde liegenden Glasfilamente brechen. Typische Formen gebündelter Fasern sind bekannt als Bänder, lose Röhrchen, eng gepufferte Fasern und Zip Twins. Die Anzahl der Glasfasern in jeder Einheit kann von einer einzelnen Glasfaser bis zu 32 oder mehr reichen, wobei Redundanz und eine Erhöhung des Bedarfs berücksichtigt wird.
9. Die Verfahren zur Vervollständigung dieser unterschiedlichen Formen verpackter Fasern umfassen die mit Gelee gefüllte Rohrextrusion, die so genannte S-Z-Verseilung, die Rohrextrusion, die Farbbandfärbung, die Verseilung mit Materialien wie Kevlarfäden und so weiter.
10. Auch bei diesen Prozessen gibt es spezielle Instrumente, um im Prozess zu messen und Kontrollmöglichkeiten zu haben, Produktparameter zu sichern wie Außendurchmesser, Innendurchmesser, Wandstärke, Konzentrizität, Faserlänge und Oberflächenbeschaffenheit. Zu den Instrumenten gehören Vorrichtungen wie Laser-Durchmessermessgeräte, Detektoren für Klumpen- und Einschnürungsflächen, berührungslose Geschwindigkeits- und Längenvorrichtungen, Ultraschall-Wanddickenvorrichtungen.
Einzelheiten zum Vorformen
Der Schlüssel zur Herstellung hochwertiger Glasfasern ist die Kombination hochreiner Materialien. Die Faser kann entweder „direkt gezogen“ oder aus einer Vorform gezogen werden, bei der es sich im Wesentlichen um einen mehrschichtigen, reinen „Glas“-Rohling handelt. Direct draw wird von den großen Faserherstellern nicht mehr verwendet. Aufgrund der hohen Dämpfung der durch diese Verfahren erzeugten Faser ist es schwierig, keine Verunreinigungen einzuführen.
Die beiden wichtigsten direkten Ziehverfahren sind erwähnenswert: Das Doppeltiegelverfahren umfasst das Ziehen des geschmolzenen Kernglases durch einen inneren Tiegel und das geschmolzene Mantelglas durch einen äußeren Tiegel. Der Hauptvorteil dieser Methode ist, dass unendlich lange Fasern gezogen werden können, solange die Tiegel ständig nachgefüllt werden. Auf diese Weise können sogar Step-/Graded-Index-Fasern gezogen werden. Bei der Rod-in-Tube-Methode wird ein Stab aus hartem Kernglas in ein Rohr aus hartem Mantelglas gelegt. Das Ende der Baugruppe wird erhitzt und als Ergebnis kann das erweichte Glas gezogen werden. Es ist wichtig, dass die beiden Glastypen ähnliche Erweichungstemperaturen haben.
Bei der Methode mit interner Abscheidung (IVD) wird eine Röhre aus hochreinem Siliciumdioxid auf einer mit einem Sauerstoff-Wasserstoff-Brenner ausgestatteten Glasdrehbank montiert. Die Chloride und Sauerstoff werden von einem Ende des Rohrs eingeführt und durch die Wärme des Brenners umgesetzt. Die resultierenden Rußpartikel – es sind Submikron-Teilchen aus Siliciumdioxid und Germanium – werden im Rohrabfluss des Brenners abgeschieden. Wenn der Brenner die Ablagerungen passiert, werden sie zu festem Glas verglast. Das Brechungsindex-Profil wird Schicht für Schicht von außen bis zum Kern aufgebaut, indem der Anteil an Silicium und Germaniumchlorid variiert wird (je mehr Germanium, desto höher der Brechungsindex). Vorteile dieses Verfahrens sind, dass die Reaktion innerhalb eines Rohrs beschränkt ist und die Verglasung im selben Schritt wie die Abscheidung erfolgt.
Beim OVD-Verfahren (Outside Deposition) werden chemische Dämpfe in einer Flamme über einen als Hydrolyse bezeichneten Prozess oxidiert. Die Abscheidung erfolgt an der Außenseite eines Quarzstabs, während sich der Brenner seitlich bewegt. Wenn die Abscheidung abgeschlossen ist, wird der Stab entfernt und das resultierende Rohr wird dann zu einem anderen Prozess zum Zusammenfallen und Verglasen bewegt. Es wird gesagt, dass dieses Verfahren die beste Gleichmäßigkeit in der Mitte der Faser (Mittellinienabfall) ergibt, was mit zunehmender Lichtquelle von LED zu Laser wichtig wird.
Ein Kostenfaktor bei Faseroptik ist die Notwendigkeit, das Signal über große Längen zu verstärken. Beim Übergang von Hochleistungs-LED-Lichtquellen zu Hochleistungslasern werden diese Abstände zwischen den Repeaterstationen zunehmen. Ein Nachteil ist, dass die höhere Leistung des Lasers an der Mittellinie höhere Reinheit erfordert, da sich sonst Komplikationen ergeben. Nachdem der Vorformling via OVD- und IVD-Prozessen hergestellt wurde, sind weitere Schritte erforderlich, bevor er zum Faserziehen bereit ist. In beiden Fällen gibt es in der Mitte des Vorformlings eine Lücke (im Fall von OVD ist sie größer), die ein Zusammenfallen erforderlich macht. Bei OVD ist auch eine Verglasung erforderlich.
Zumbachs Rolle im Prozess
Bei allen drei Prozessen, IVD, OVD und VAD, ist es wichtig, die Maßvorgaben im Schichtprozess einzuhalten. Jede Schicht muss eine bestimmte Dicke und Zusammensetzung haben. Sie muss eingehalten werden, damit die fertig gezogene Faser die erforderlichen Leistungseigenschaften hat. Die zwei Hauptfunktionen, die das Durchmesser-Messgerät bietet, sind Durchmesser und Position. Der Durchmesser ist für die Bestimmung der Dicke der Abscheidungsschicht kritisch, während die Position für die Einhaltung des Abstands zwischen der röhrenförmigen Vorform und dem Abscheidungsbrenner kritisch ist, typisch zwischen 35 mm und 55 mm. Der Durchmesser nimmt mit jedem Durchgang (OVD) zu, aber die Brennerposition relativ zur Außenfläche des Vorformlings muss konstant sein.
Dimensionell ausgedrückt bedeutet dies: Je größer der Durchmesser des Vorformlings ist, desto länger kann eine einzelne Faser daraus gezogen werden. Der Nachteil hierbei ist, dass die Dämpfung mit dem Durchmesser des Vorformlings zunimmt. Dies begrenzt die Faserlänge. Da die Prozesse hier verfeinert werden, kann davon ausgegangen werden, dass die Durchmesser der Vorformlinge proportional zunehmen. So ergibt eine Vorform mit 80 mm Durchmesser eine Einmodenfaser mit einer Länge von 400 km und einem Durchmesser von 0,125 mm.
Sowohl IVD als auch OVD setzen bei der Preform-Herstellung auf die „Faser-Drehmaschine“. Diese ist im Wesentlichen identisch mit einer Maschinendrehbank, wobei Drehfutter die Enden des „Werkstücks“ halten, in diesem Fall ein Quarzrohr. VAD ist ein Sonderfall, da die Ablagerung axial in einer halbversiegelten Kammer („Vorzerstäubungs-Sprühkammer“) auf einem vertikalen Turm erfolgt. Diese massiven Strukturen sind mehrere Stockwerke hoch. Bei diesem Verfahren werden alle Abscheidungsschichten in einem Durchgang mit mehreren Brennern aufgebracht, die jeweils für eine Schicht (Kern, Mantel usw.) verantwortlich sind. Der Vorformling wird oben und unten mit Aufhängestangen (auch Quarz) verschweißt, die dann in oberen/unteren Spannfuttern im Turm platziert werden. Der Vorformling wird gedreht und gleichzeitig zwischen den beiden Turmfuttern gezogen, um den gewünschten Durchmesser und die gewünschte Schichtdicke zu erhalten.
VAD erfordert einen Durchmesser-Scanner, um durch ein Objektglas zu messen. Hitzeschilde werden empfohlen, sind jedoch nicht erforderlich (beachten Sie, dass die Kammertemperaturen 3000 °C erreichen). Der Durchmessermesser muss in der Lage sein, den genauen Durchmesser entlang der Vorform abzulesen und auch den Übergangspunkt zwischen den Quarz-Aufhängungsstangen und der tatsächlichen Vorform (ermittelt durch Durchmesseränderung) zu finden.
Faserzeichnung im Detail
Mit der Herstellung des Vorformlings zieht die Herstellung fort, die optische Glasfaser aus dem Vorformling zu ziehen. Dies wird erreicht, indem die Vorform oben auf einem Ziehturm angeordnet wird und das Glas mit Wärme erweicht wird, so dass es beginnt sich zu verflüssigen. An diesem Punkt bildet sich eine Kugel aus geschmolzenem Glas am Boden der Vorform, die dann durch die Maschine zu einer Aufwickelspule geführt wird. Wenn die Spezifikationen erfüllt sind, wird das Ende (Glaskugel) entfernt und die verbleibende Faser wird auf Rollen gelegt. Die verschiedenen Stufen dieses Prozesses werden nachfolgend erläutert.
Es gibt scheinbar endlose Permutationen bezüglich der Arten und Marken von Fasern, die mit diesen Verfahren hergestellt werden, aber alle Fasern können in zwei große Kategorien eingeteilt werden: Einmodenfaser und Multimodefaser. Der Wortmodus beschreibt einen unabhängigen Lichtweg durch eine Faser. Daher bezieht sich „Einzelmodus“ auf Fasern, die nur einen Pfad zulassen, und „Multimodus“ bezieht sich auf Fasern, die viele zulassen. Meist wird die Singlemode-Faser für Fernübertragungen (km) verwendet, und der Multimodus wird für kürzere Distanzen (2000 m oder weniger) verwendet, obwohl diese Regeln nicht in Stein gemeißelt sind.
Alle Fasern umfassen einen Kern und eine Mantelschicht, deren Abmessungen während des Vorformungsstadiums bestimmt werden. Der Außendurchmesser beider Arten von gezogenen Fasern beträgt 125 µm, bestehend aus dem Kern, der die Lichtwellen trägt, und der Ummantelung. Die schützenden UV-Beschichtungen variieren stark, bringen jedoch normalerweise einen Enddurchmesser zwischen 250 µm und 900 µm.
Typisch hat die Einmodenfaser einen Kerndurchmesser von 8 µm, was eine Ummantelungsschicht mit einer Dicke von ungefähr 58,5 µm erfordert. Multimode-Faserkerne können buchstäblich jede Dimension haben, gängige Kerndurchmesser sind jedoch 50 µm und 62,5 µm. Der größere Kern der Multimodefaser ermöglicht viele weitere Pfade (Modi) für das Licht. Der Kompromiss ist jedoch eine höhere Dämpfung der Lichtwelle (Licht wandert größere Entfernungen pro Längeneinheit der Faser). Der Einzelmodus beschränkt die Anzahl der Pfade (Modi) auf nur einen, führt jedoch zu viel größeren Übertragungsdistanzen zwischen der Regeneration des Signals.
Ein Teilschritt beim Faserziehen ist das Einfärben der Faser durch Aufbringen von UV-gehärteten Tinten. So kann jede Faser anhand ihrer Farbe in Bezug auf Typ, Größe und Leistung identifiziert werden. Beispiele zeigen einen Faserschubmast, lose Schlauchkabel in einem mehradrigen Glasfaserkanal, der das Blasen (Installieren im Feld) weiterer Faserkabel ermöglicht. Dies erfolgt mit Hilfe einer Druckluftquelle, um das Abführen der Faser durch die bereits installierte Leitung zu unterstützen.
Bruno Mühlheim ist freier Journalist in Orpund/Schweiz
Zumbach Electronic AG
2552 Orpund/Schweiz
Ansprechpartner Herr Daniel Frankum
Tel.: +41 32 3560400
sales@zumbach.ch
www.zumbach.com